Locations
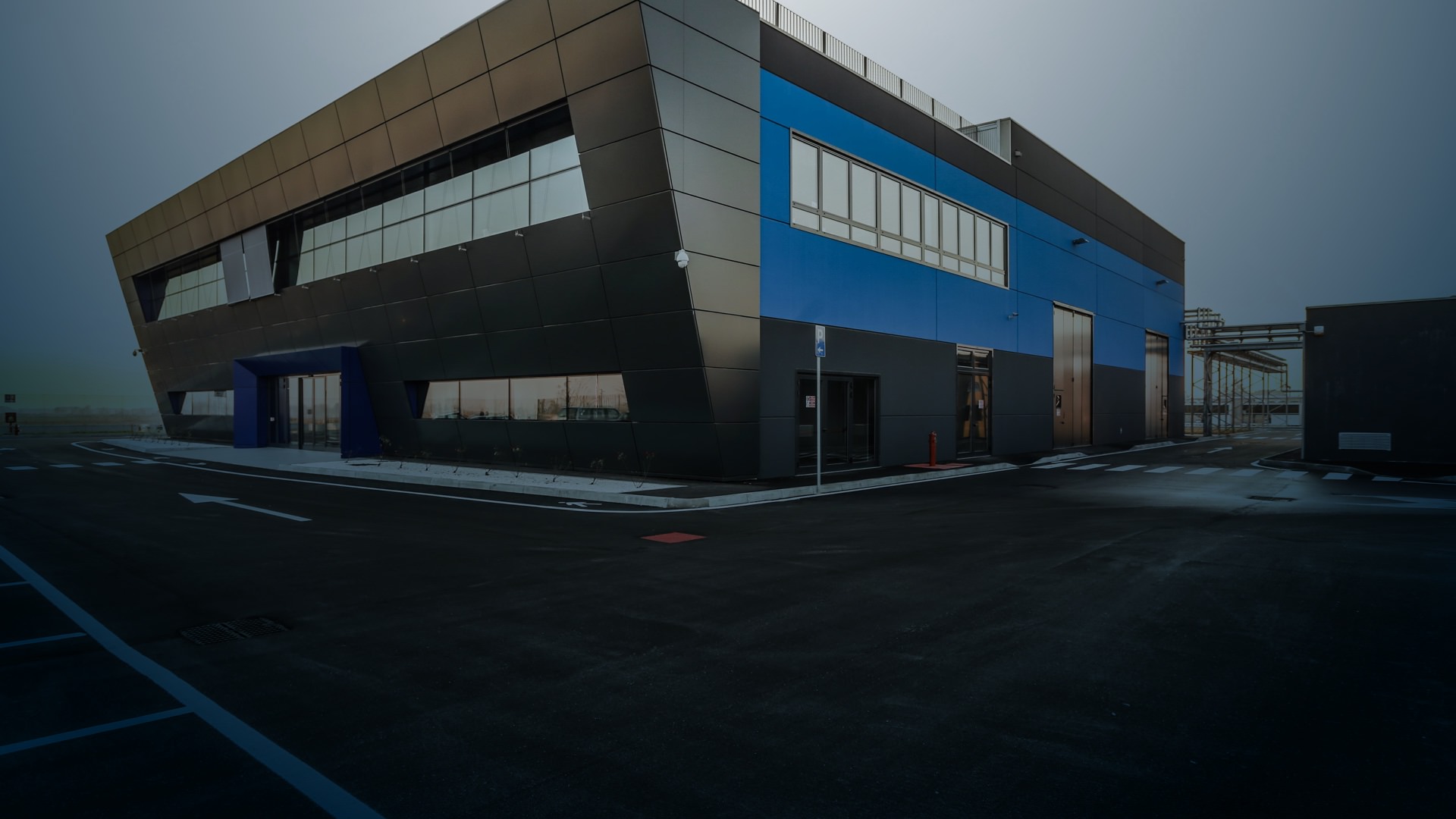
#PlantsInEurope
Avio Aero has state-of-the-art manufacturing facilities and laboratories across Europe: in Italy, Poland and Czech Republic.
Avio Aero Plants
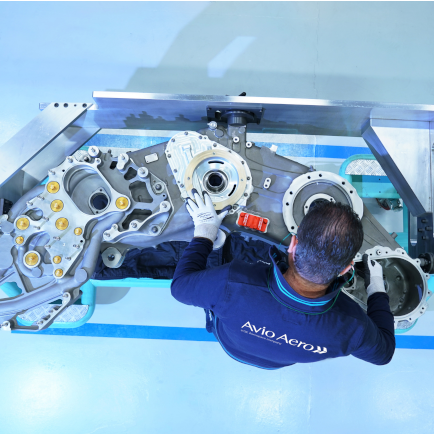
In Rivalta, we have our headquarters and main production site. Here, we design and manufacture power and accessory gearboxes, entire transmission systems, low-pressure turbine modules, rotating components for aviation engines, as well as automation and electronic simulation systems.
The plant receives gearbox housings from our foundry in Borgaretto, and we carry out all machining processes, gear production, and testing. These efforts culminate in the delivery of gearboxes and transmissions that power the world's most widely used aircraft. Additionally, this site is the main hub of our research and development activities, defining the key enabling technologies for next-generation propulsion systems, including Avio Aero-led projects in Clean Aviation.
Contacts:
Via I Maggio 99 - 10040 -
Rivalta di Torino (TO) - Italy
+39 011 0082111
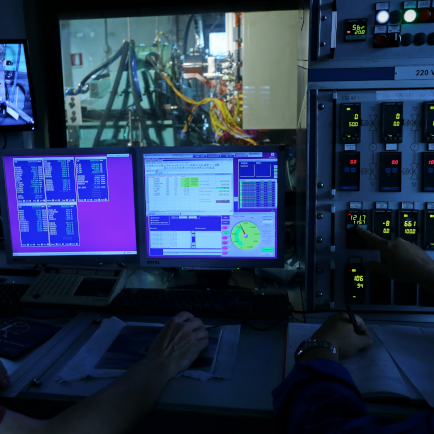
It is one of the Avio Aero testing sites that has been performing development and certification tests on engines, modules, and components for the most important civil and military aviation programs for more than 60 years.
The site is currently focusing on experimental testing of power gearboxes, accessory gearboxes, accessory drive trains, and accessory modules such as oil pumps. The tests performed on these modules include vibration surveys, endurance tests, attitude tests, torsional dynamics tests, and start mode testing, also with the aid of telemetry. The site also conducts fluid dynamics and aeroacoustics tests on a number of rigs, laboratory mechanical tests on components, turboshaft engine tests, and the design and application of instruments in a specially created laboratory.
Contacts:
Strada del Drosso, 145 - 10135 -
Torino (TO) - Italy
+39 011 0082111
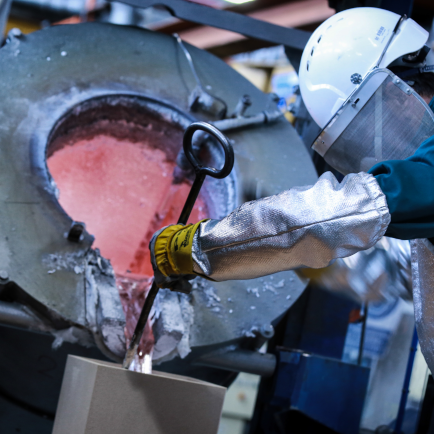
The plant has two product centers: the first is the foundry, which performs casting processes from sand mold creation to the casting of aluminum and magnesium alloys; the second center carries out the finishing processes on the castings produced, including heat treatments, welding, and testing.
In Borgaretto we produce oil tanks, oil pumps, and mechanical gearbox housings for major civil and military aviation programs. The magnesium casting area produces components for specific applications, such as the EJ200 engine installed on the Eurofighter Typhoon fighter jet, which require extreme strength combined with light weight.
Contacts:
Via Rondo Bernardi, 15 - 10092 - Borgaretto di Beinasco (Torino) - Italy
+39 011 0054111
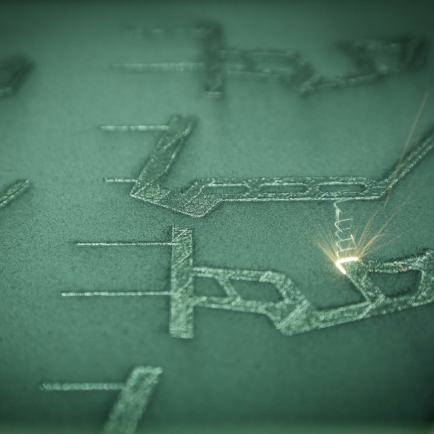
Opened at the end of 2013, this plant is dedicated to the production of aviation engine components using additive manufacturing technology, a state-of-the-art technique capable of producing solids of any shape starting from a digital model by combining special metal alloys from powders.
The EBM (Electron Beam Melting) technology is used in this plant, where metal powders are melted by means of an electron beam. The process utilizes metallic powders of TiAl alloys, intermetallic materials consisting mainly of titanium and aluminum.
Contacts:
Strada Privata Gabrielli 3 - 28062 - Cameri (NO) - Italy
+39 011 0082111
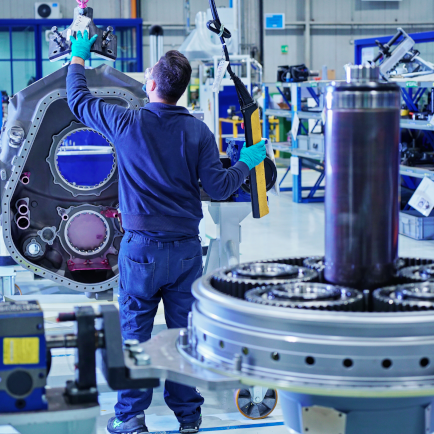
The plant has three product centers and Europe's biggest engine test room. It has a well-recognized history in manufacturing low-pressure turbine stator and rotor blades, as well as combustion chambers for the most important civil and military aviation programs, including the GEnx, GE9X, Catalyst, EJ200, and LEAP.
The combustor of the LEAP, with its groundbreaking double wall chamber, is built exclusively at this site. The CRO (Component Repair and Overhaul) services for components designed and produced by Avio Aero are also based here.
Contacts:
Viale Giuseppe Luraghi, 20 - 80038 -Pomigliano d’Arco (NA) - Italy
+39 081 3161111
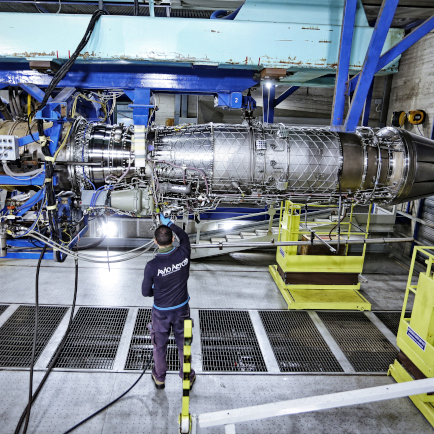
The plant has always specialized in the assembly and maintenance of aviation engines, particularly for the Italian Air Force. Here, the EJ200 engine of the Eurofighter Typhoon and the GE CT7-8E6 turboshaft engine for the Italian Armed Forces’ helicopters are assembled and maintained.
Additionally, we produce components for the low-pressure turbine of the LEAP, GEnx, and GE9X engines. In the Additive Manufacturing area of the plant, we manufacture 3D-printed components for the Catalyst turboprop engine.
Contacts:
Via Angelo Titi, 16 - 18 - 20 - 72100 -
Brindisi - Italy
+39 0831 556111
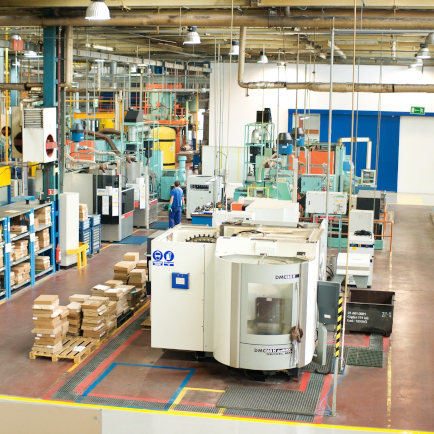
At this site we produce stator and rotor blades for low pressure turbines for civil and military engines, including GE90, GEnx 1 and 2b, CFM56, T700, PW308 and LEAP. For the LEAP, the plant manufactures the low pressure turbine nozzles and stator turbine blades for stages 3, 4 and 5 on all three versions of the engine (LEAP-1A, -1B and -1C).
Contacts:
ul. Grażyńskiego 141 43-300
Bielsko-Biała - Poland
+48 33 813 40 12 / +48 33 813 21 27
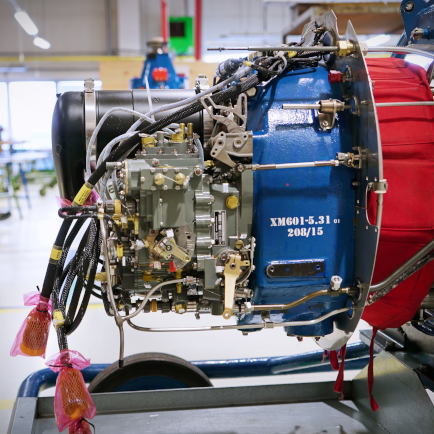
This is our Turboprop engine center of excellence. The plant is responsible for the design, production, and testing of the H-Series family and M601, as well as the assembly and testing of the Catalyst turboprop engine.
Contacts:
GE Aviation Czech, s.r.o., Beranových 65, 190 00 Prague 9, Czech Republic
+420 222 538 111